At Briess, sustainability is not just a buzzword, but a deeply ingrained value that drives our operations and innovations. As part of our ongoing commitment to environmental responsibility, we’ve taken significant strides to reduce waste, optimize energy usage, and ensure that every step of our malt production process aligns with sustainable practices.
In this report, we look back on some of the key initiatives that have shaped our sustainability efforts over the past year. From improving barley cleaning processes to optimizing water usage and reducing energy consumption, we are proud of the progress we’ve made in minimizing our environmental impact. Through collaboration with local farmers, strategic upgrades to our equipment, and creative partnerships, Briess continues to lead the way in crafting high-quality malt while safeguarding our planet for future generations.
Join us as we reflect on the results of these impactful projects and celebrate the positive changes that are making a difference—one step at a time.
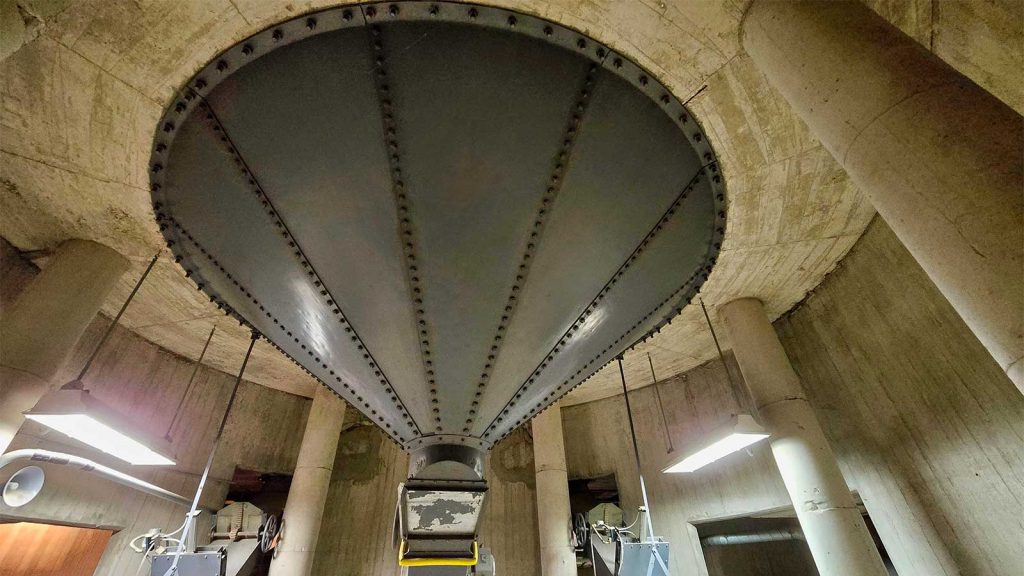
of the transfer lines to minimize barley and malt breakage and ensure gentle transfer.
Project: Improved Barley Cleaning Process
Summary:
Year-round, we work with local farmers to ensure that sound grain, which does not make the cut for malting and brewing, still gets to be utilized in our local community feeding animals. While we all love our local farmers, our primary focus is making great malt for you to enjoy to the last sip! We looked at our barley cleaning process end-to-end and evaluated each site: from receiving at the rail to cleaned barley ready to malt. We establish the quality of barley we want and what is happening to barley at each step. This included adjusting feed rates and tearing down machines to find tiny gaps where barley could sneak through and fall to animal feed or waste rather than completing its journey further onto malting. With a plant that spans along quite a bit of the lakeshore, this was quite the undertaking! We also implemented new level feeds and variable frequency drives (VFDs) to reduce how much time the machines were in use. Even more energy savings we could calculate!
Annual Savings:
A whopping 1.1 million pounds diverted from animal feed – that’s 22 truckloads!
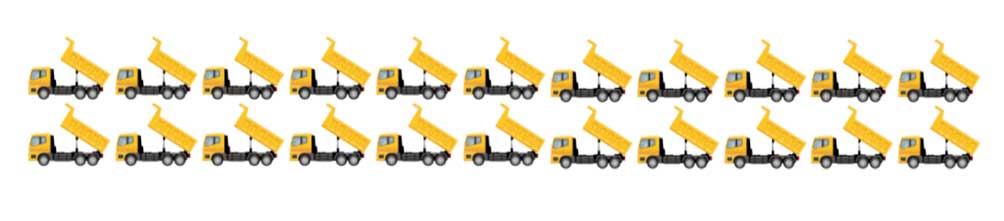
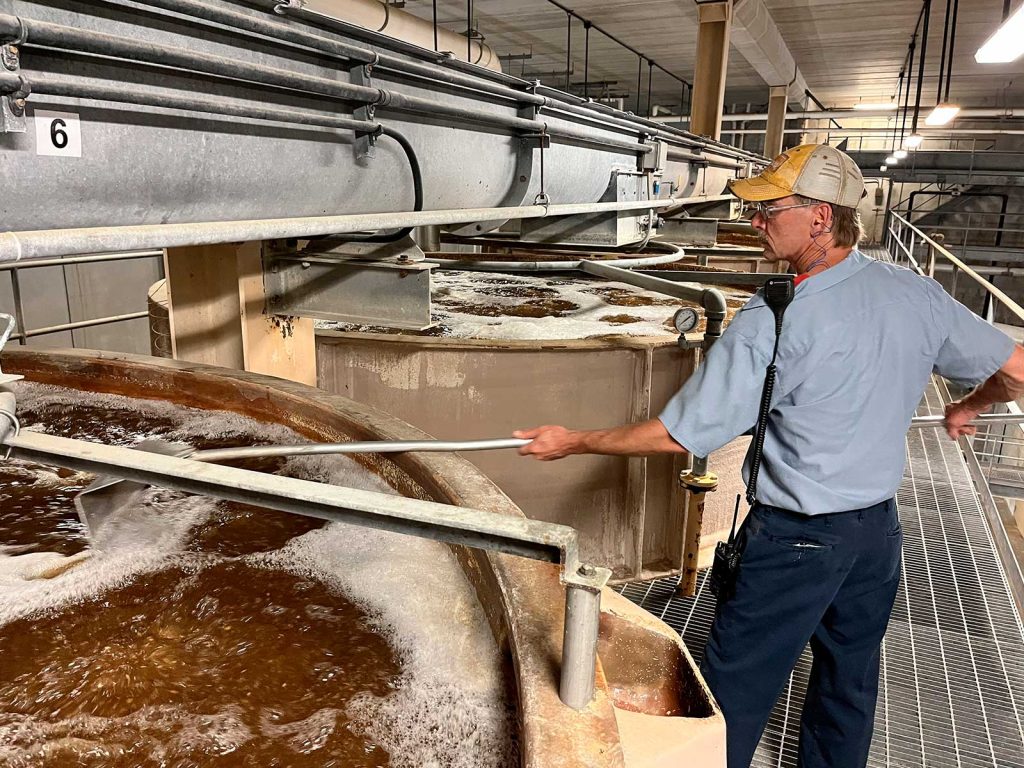
for barley chit, the first sign of a growing seed.
Project: Water Usage Audit and Optimization
Summary:
We all know that brewing and malting use a lot of water! We are growing tiny plants and they are thirsty! Water reduction has been a focus of Briess with a special focus across all the malthouses. Optimizing water transfers, and sanitation, and increasing our depth of knowledge on moisture behavior within barley has allowed our team to seamlessly reduce water while maintaining the Briess quality you expect! Water must be chilled or heated depending on purpose: less water usage equals less energy needed to change the temperature for the purpose.
Annual Savings:
Over 6.3 million gallons; we could use that saved water to fill 9 Olympic pools!
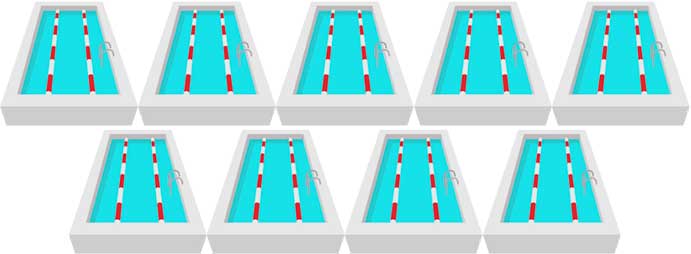
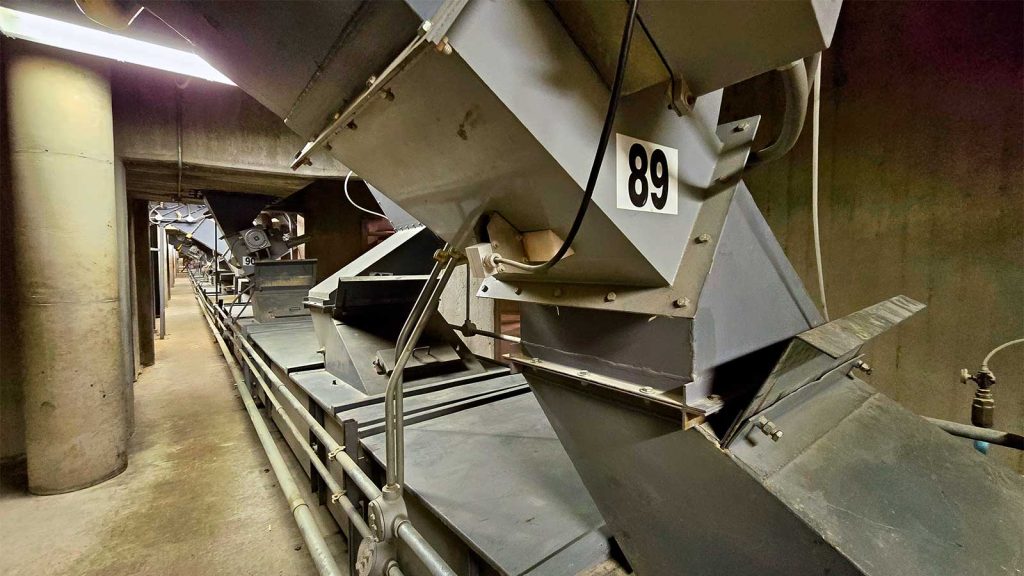
Project: Grain Handling Improvement
Summary:
Our barley and malt take a long journey once inside our malthouse. These grains travel through rail or boat to receiving, through legs to bins, from bins to steep tanks, from steep tanks through germ beds, germ beds to kilns, kilns to roasters, roasters to bins, and bins to packaging! Through a thorough evaluation of every movement our grain takes, we were able to reroute barley and malt to minimize the journey through conveyors, valves, and bins to reduce the chance of breakage and loss. Less breakage and loss mean more barley and malt fulfilling their duty and making it to your glass!
Annual Savings:
We have diverted more than 126,000 pounds from animal feed, which is the same as the weight of 90 average dairy cows!
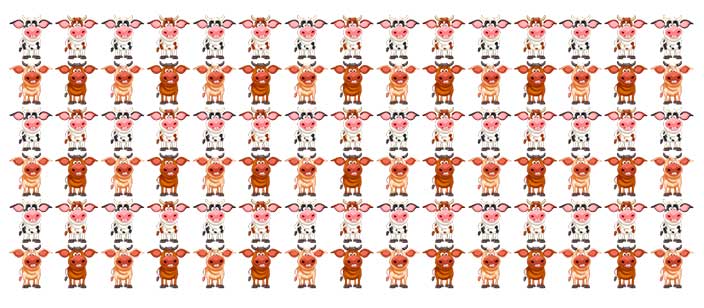
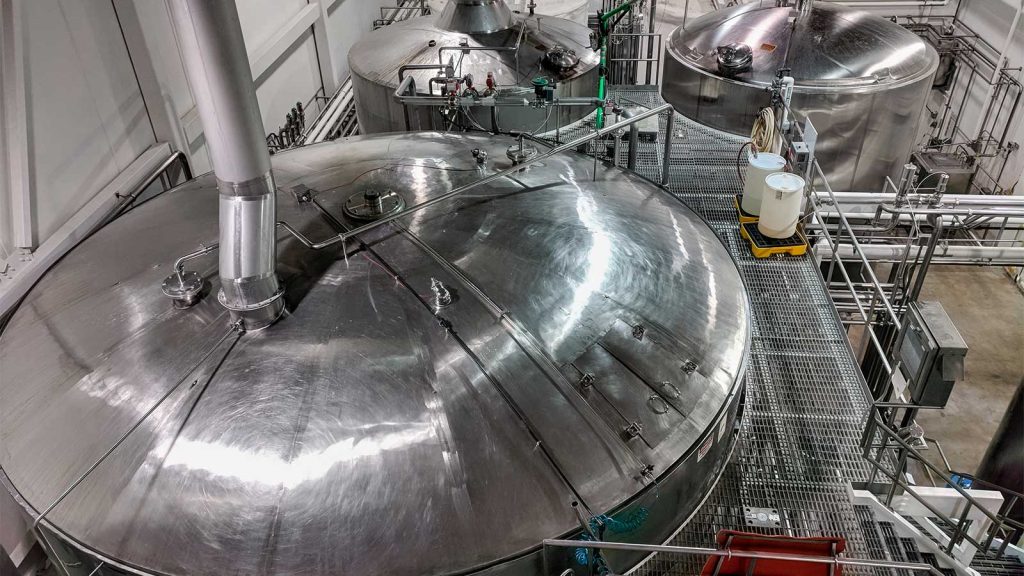
Project: Improved Efficiencies
Summary:
We implemented a series of continuous improvement projects with a united goal of increasing capacity, reducing resources needed per pound of material, and improving wash efficiencies to reduce the number of rinses and chemical use. Operations and Technical Services worked hand-in-hand to look at the liquor-to-grist ratio needed to mash in our brewhouse. With some innovative thinking and extensive trials, the team came up with recipe cadence adjustments that allowed water to be saved.
Annual Savings:
This project saved 122,000 therms of gas and over 1.5 million gallons of water! That’s over 66 cars driven around the entire circumference of the earth and over 2 Olympic pools!
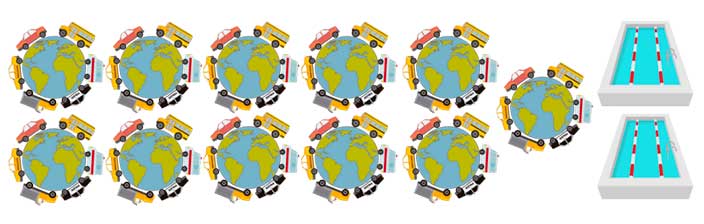
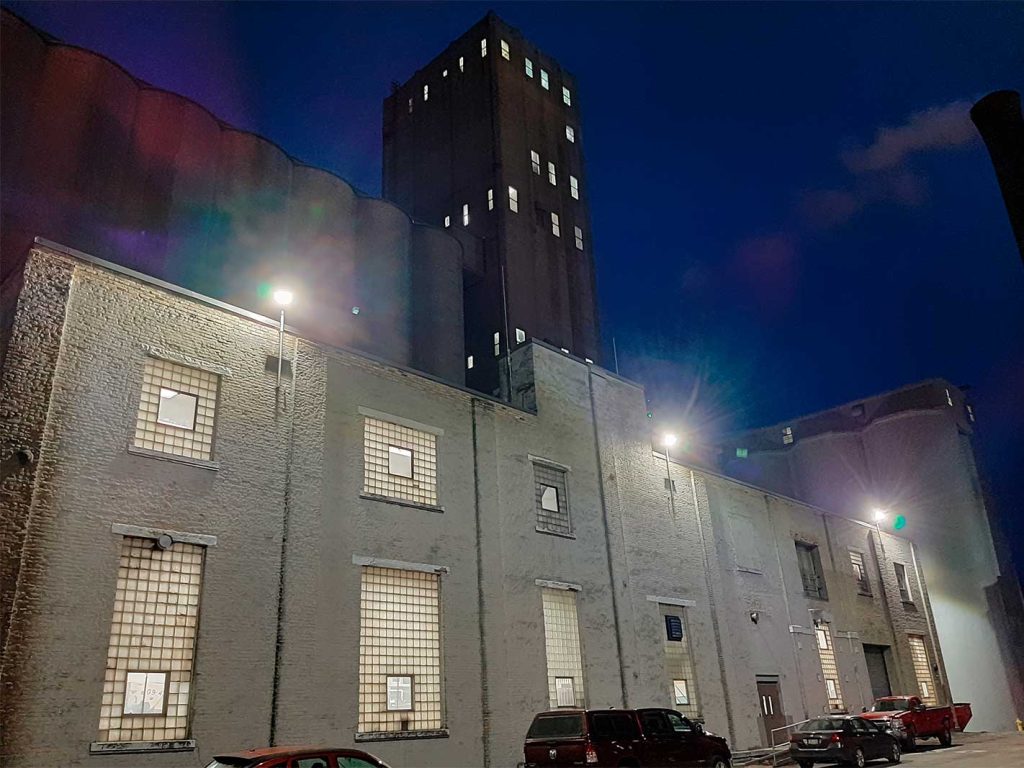
Project: Lighting and Conveyor Upgrades
Summary:
Historic buildings have historic lighting, which is not historically very efficient. Briess performed an energy audit across the company finding lighting opportunities. Installing occupation sensors and dawn-to-dusk sensors to help automatically reduce Briess’s energy consumption was a no-brainer for us! Briess also found conveyors that benefitted from using sensors to minimize their footprint!
Annual Savings: That’s 97,151 kilowatt hours or over 33 electric cars being driven for an entire year!
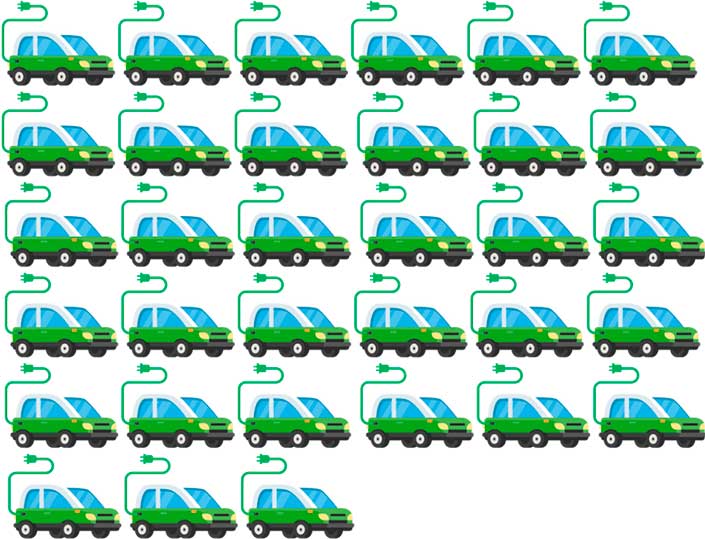
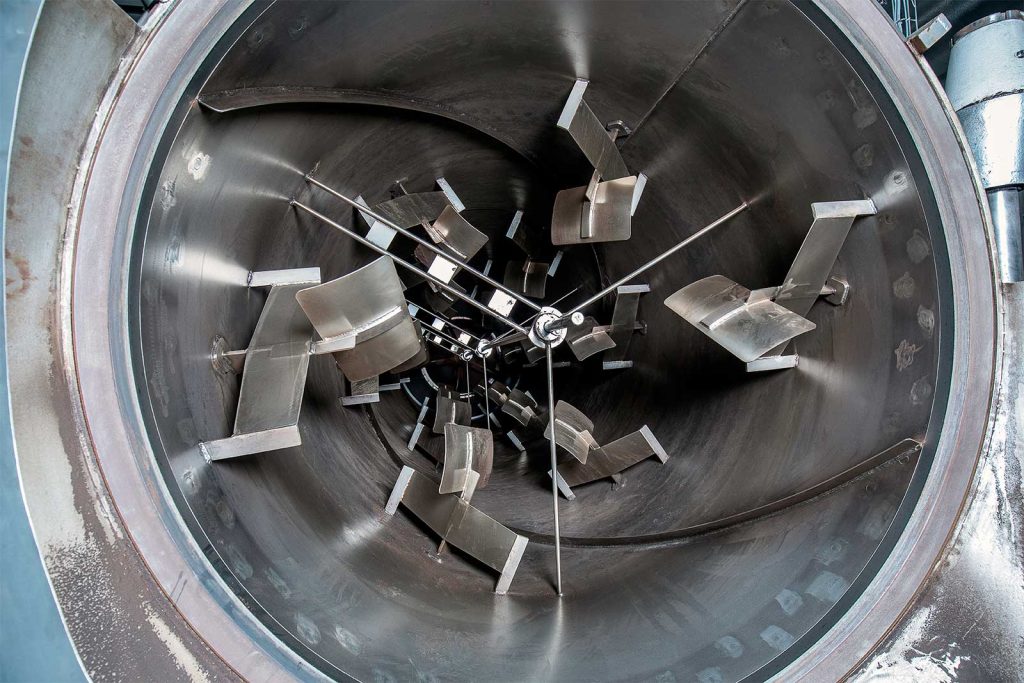
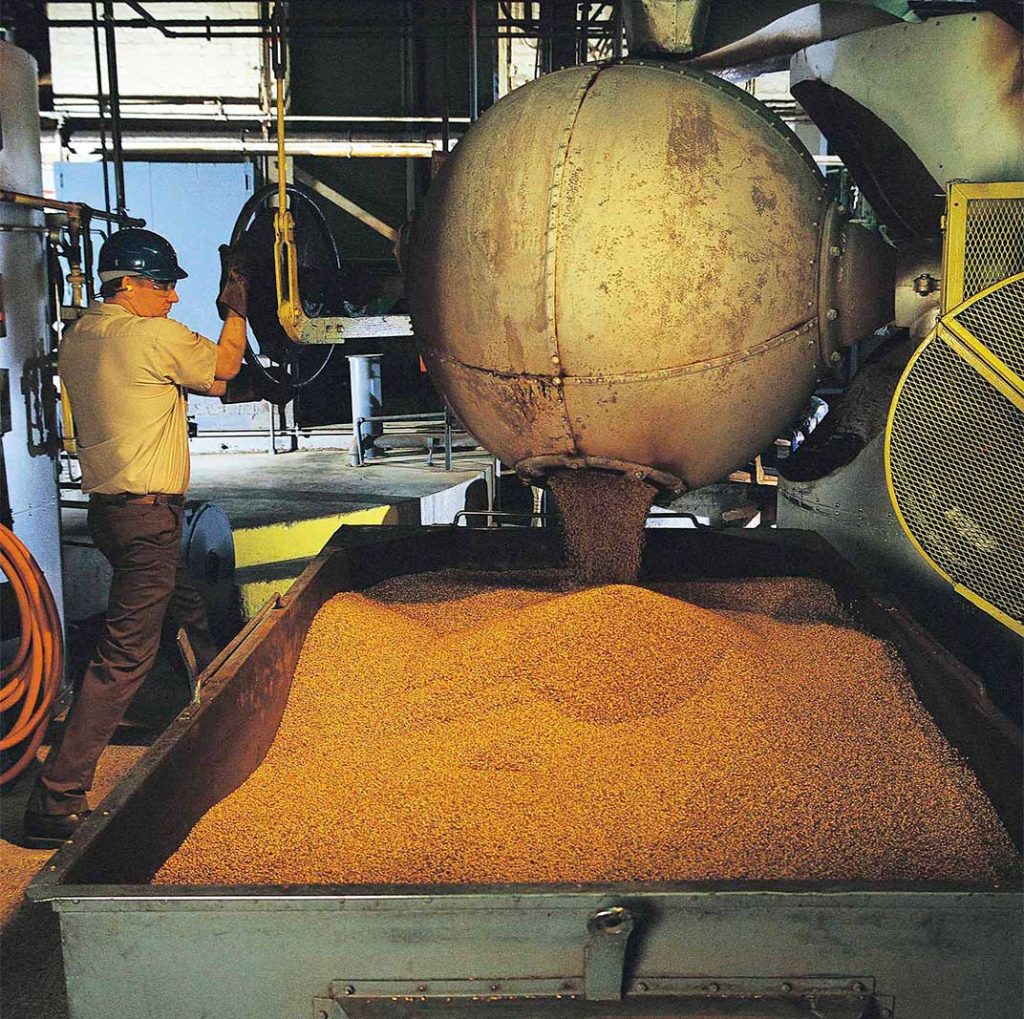
Tom Pfeffer empties a K-Ball roaster, circa 1970.
Project: Roasting Efficiencies
Summary:
Briess has come a long way since the K-Ball roasters of our specialty malt origins! These roasters were heated by an open flame directly on the outside of the K-Ball roaster! While this is not the first roaster upgrade for our team since the K-Ball, this roaster upgrade comes along with a 20% efficiency improvement over the incumbent (and many fold beyond that from the K-Ball!)! This efficiency also includes an increase in capacity allowing Briess to process more pounds per energy use including the operational overhead energy used to power our buildings and control our buildings’ temperatures. Heating uses energy and the type of heating matters. With radiant, conductive, and convective heating methods, having the right blend assures our malt maintains our high standards for quality, while also reducing our natural gas consumption.
Annual Savings:
That’s 20% less energy used during drying, compare that 20% to a big chunk of grandma’s pumpkin pie!
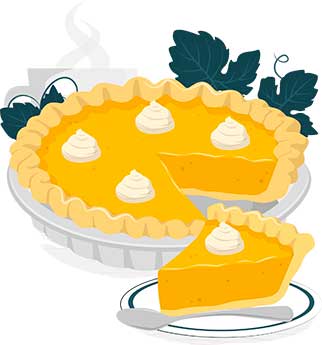
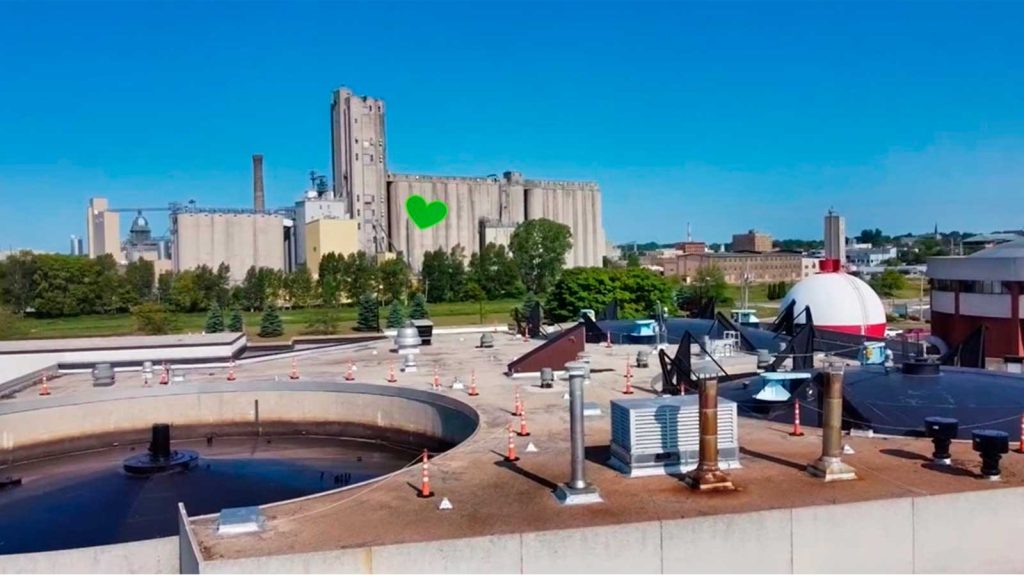
Photography credit: https://youtu.be/SqNP-sehpM4
Project: Manitowoc Public Utilities Partnership
Summary: Why waste your waste? We partner with Manitowoc Public Utilities (MPU) and our very own Betsy Roberts, Director of the Center of Malting Excellence for Briess, is on their board! MPU puts our wastewater to use, feeding anaerobic bacteria that create methane gas which is used within MPU. The anaerobic bacteria also create hummus-like material that can be used as a fertilizer for agricultural crops. MPU has sustainable initiatives at the forefront of their thinking – they have been converting boilers over from traditional fossil fuels to Wisconsin-recognized renewable fuel pellets. These fuel pellets can be made from local paper industry waste streams! Over the last 3 months, on the days that MPU has had to generate power, MPU has used the fuel pellets exclusively!